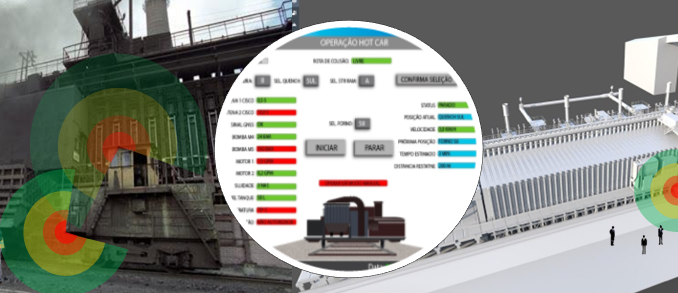
A automação de processos industriais tem se mostrado uma tendência cada vez mais presente na busca por eficiência, produtividade e segurança.
No setor de produção de aço, a automação do posicionamento de Hot Cars, surge como uma oportunidade para melhorar o processo de operação dessas máquinas, aumentando a precisão, linearidade e eliminando desvios operacionais.
O objetivo deste projeto foi propor uma solução abrangente que visa automatizar não apenas o movimento dos Hot Cars, mas também implementar um novo conceito de operação, permitindo que os operadores interajam mais com a interface homem-máquina (IHM) interna da máquina, em vez de usar as alavancas existentes.
A solução proposta inclui vários pacotes de produtos funcionais que se complementam:
Anticolisão com a máquina de abertura (DoorMachine): Essa funcionalidade utiliza a condição de Hot Box totalmente recuada como intertravamento para o movimento semiautomático, evitando colisões com a DoorMachine. O movimento só é permitido quando essa condição é atendida, caso contrário, o movimento é bloqueado até que a condição seja normalizada.
Anticolisão com o êmbolo estacionário (STR RAM): Esse pacote utiliza a leitura do GPS e dos radares instalados no Hot Car para assegurar que as máquinas não colidam com o êmbolo estacionário. Os dados do GPS e dos radares são processados pela RPU (Unidade de Processamento Remoto), por meio do software LYNX CORE, e encaminhados para o PLC (Controlador Lógico Programável), que aplica lógicas para permitir ou bloquear o movimento da máquina. Em caso de proximidade detectada, a velocidade é reduzida e, em seguida, o movimento é bloqueado. Na tela de operação, um pop-up é exibido para que o operador confirme o término do movimento, verificando se o êmbolo está realmente retraído. Essas ações ocorrem em distâncias pré-definidas.
Anticolisão contra pessoas em rota de colisão: Essa funcionalidade adiciona recursos para evitar colisões entre pessoas que estejam em rota de colisão com o Hot Car, aumentando a segurança operacional.
Posicionamento semiautomático do Hot Car: Essa solução de posicionamento baseia-se na utilização de informações dos GPS instalados para obter a posição georreferenciada das máquinas.
Com base nessas informações de posicionamento, as lógicas necessárias podem ser implementadas. Os dados do GPS são processados pela RPU, por meio do software LYNX CORE, e disponibilizados para o PLC.
Quando o operador seleciona o movimento desejado por meio da IHM, os dados processados são utilizados para gerar as instruções que o PLC deve executar para movimentar a máquina até a posição desejada. Essa funcionalidade requer alterações nas conexões elétricas para permitir a operação automática de posicionamento, substituindo as alavancas existentes. Além disso, são utilizados sinais de vazão do sistema hidráulico do Hot Car para calcular a velocidade equivalente e integrá-la para obter o deslocamento do veículo. Essa variável permite o funcionamento semiautomático em momentos em que o sinal do GPS não esteja disponível. Também é necessário levar o sinal do pedal de freio para o PLC, a fim de obter um posicionamento preciso do carro em relação às posições de destino.
Desenvolvimento de tela na IHM: Uma nova tela é desenvolvida na IHM GTO6310 da Schneider para apresentar um console de operação, onde o operador pode selecionar o modo de operação da máquina (manual ou semiautomático), escolher o movimento desejado para a movimentação semiautomática (ir para os fornos, torre de resfriamento ou garagem) e iniciar o movimento. Além disso, a tela permite monitorar variáveis relacionadas ao processo de translação, bem como diagnosticar instrumentos e intertravamentos do sistema. A tela também exibe alarmes configurados, como resumo de falhas, despoeiramento desligado, falha no rádio Cisco e baixa carga da bateria do Hot Car.
Os radares são utilizados para a interface de anticolisão, fornecendo leituras que permitem a geração de sinais de redução de velocidade e intertravamento dos movimentos de translação. A região de calibração do radar é ajustada de acordo com o formato do equipamento. Se alguma leitura do radar ultrapassar essa região, a lógica do sistema ativa redução de velocidade ou bloqueio dos movimentos do equipamento.
O radar possui uma porta CAN para conexão de dados. No painel onde está localizada a RPU, um conversor CAN/Ethernet converte a rede CAN do radar em rede Ethernet TCP/IP. Esse conversor é conectado ao switch Ethernet do painel, fornecendo os dados para a RPU.
Para o funcionamento do posicionamento semiautomático, é fundamental o uso de dados precisos e confiáveis. Nesse sentido, a integração de variáveis de posição provenientes do GPS e da velocidade do Hot Car desempenha um papel crucial. Ao considerar que o sistema hidráulico do Hot Car modifica a vazão de acordo com a abertura da válvula de acionamento, é possível estabelecer uma correlação direta entre a vazão e a velocidade da máquina. Isso possibilita a obtenção da velocidade por meio da análise da vazão e da porcentagem de abertura da válvula.
Em situações em que o sinal de GPS está indisponível, a posição integrada por meio da velocidade surge como uma importante redundância. É comum ocorrerem momentos em que o sinal do GPS é comprometido, seja devido a interferências externas ou a problemas técnicos. Para lidar com essa indisponibilidade momentânea do sinal, é necessário estabelecer mecanismos de segurança. Um alarme na IHM pode ser acionado para alertar os operadores sobre a falta de sinal. Após um período pré-definido sem o retorno do sinal, o modo semiautomático fica temporariamente indisponível. Durante esse intervalo, a posição integrada serve como referência, sendo corrigida assim que o sinal do GPS for restabelecido.
A definição das posições dos fornos e das torres de resfriamento é um passo essencial no processo de automação do posicionamento de Hot Cars. Essas posições devem ser cadastradas no programa do Controlador Lógico Programável (PLC). Quando um operador seleciona a bateria, o número do forno ou a torre de resfriamento desejada, o programa consulta as posições cadastradas e indica o destino do movimento. Essa funcionalidade simplifica a operação e permite que o Hot Car seja movido com precisão para a posição desejada.
Uma função importante incorporada ao sistema de posicionamento é a autocalibração. Essa função permite ao operador corrigir manualmente a posição do Hot Car caso identifique uma divergência em relação à posição destino. Após reposicionar a máquina manualmente e abaixar o Hot Box, a nova posição é salva e substitui a posição anteriormente cadastrada. Isso garante a precisão do posicionamento e a correção de eventuais desvios.
Conclusão
A utilização de dados integrados para o posicionamento semiautomático de Hot Cars representa um avanço significativo na automação do setor siderúrgico. A integração das variáveis de posição e velocidade permite contornar a indisponibilidade temporária do sinal de GPS, garantindo a continuidade das operações com segurança e precisão.
O cadastramento de posições e a função de autocalibração complementam essa abordagem, tornando o sistema ainda mais confiável e eficiente. Com a implementação dessas inovações, é possível elevar o desempenho e a produtividade das operações envolvendo Hot Cars, promovendo um ambiente de trabalho mais seguro e eficaz.
Agora que você finalizou este artigo, aproveite e descubra sobre O impacto de sistemas autônomos no design e engenharia de máquinas aqui.